Elon Musk was right in all his predictions when he abandoned a carbon starship to convert it into steel
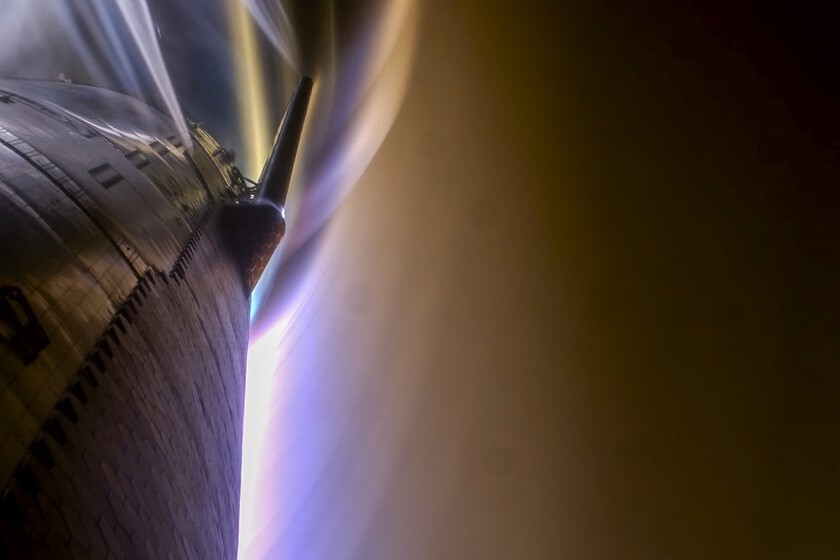
The decision to switch from carbon fiber and aluminum to stainless steel when building Starship proved to be a make-or-break decision for SpaceX.
Starship is the first stainless steel rocket to reach space since the Atlas program in the 1950s. SpaceX didn’t always plan to use this material: it was a risky bet by Elon Musk that ended up working incredibly well.
Reusable rocket. Starship 29 survived reentry on Flight 4 despite friction with air at 20,000 kilometers per hour. He lost many thermal tiles and most of his spoiler when plasma began leaking through the rocket’s joints.
However, he restarted the engines, went vertical and simulated a landing in the Indian Ocean using half-melted ailerons. The reusable rocket failed to be destroyed upon reentry, despite the loss of part of its ceramic heat shield. The steel resisted.
From BFR to Starship. Around the same time the rocket changed its name to Starship, Elon Musk announced that he had decided to abandon the Big Fucking Rocket’s carbon fuselage in favor of a new one made from stainless steel, namely alloy 301.
Early models of the ship looked poor due to wrinkles in the embossed material, but Musk argued that steel was the best choice for a 100% reusable rocket.
The advantages of steel. In an interview with Popular Mechanics in 2019, Musk listed the reasons for the change:
- Steel can withstand temperatures of 810°C, compared to 149°C for carbon fiber and aluminum, which would be brittle if re-entered into the atmosphere.
- Steel becomes stronger at cryogenic temperatures, such as the liquid methane that Starship uses as fuel.
- Steel is better able to resist microcracks, such as those that might occur in a rocket designed to land and fly repeatedly.
- And above all, steel costs $3 per kg compared to $200 per kg for carbon fiber.
Heat shield. The Starship design has continued to evolve since 2019. Instead of a heat shield, it was planned to again use its own steel body, actively cooled by methane, but this idea was abandoned because it made the rocket heavier.
Eventually, SpaceX added thousands of hexagonal ceramic tiles to Starship’s body as a heat shield. They are very light and crack resistant, but are able to withstand atmospheric braking, although they transfer heat to the steel underneath.
Own alloy. Another important change is that they stopped using 301 steel in favor of their own alloy, patented by SpaceX.
Commercial stainless steel had problems with “interlaminar toughness”: it did not tolerate crack propagation between layers at cryogenic temperatures; like those on takeoff when the rocket is full of methane and liquid oxygen.
The cheapest rocket. It’s unclear how much SpaceX is investing in this material, but there are already dozens of prototypes and Elon Musk is quite optimistic in his predictions about the cost of the program.
SpaceX aims to build thousands of Starships for the colonization of Mars, funding rocket development through launches of Starlink and other satellites in addition to NASA contracts for lunar missions.
Musk estimates that thanks to its 100% reusable design, the price per kilogram of Starship will be well under $100, which is 20 times less than the cost of launching a kilogram on Falcon 9.
Image | SpaceX
In Hatak | Elon Musk has calculated what is needed to build a sustainable city on Mars: 1000 starships and 20 years of launches