Inditex and Basf present a jacket made from recycled nylon
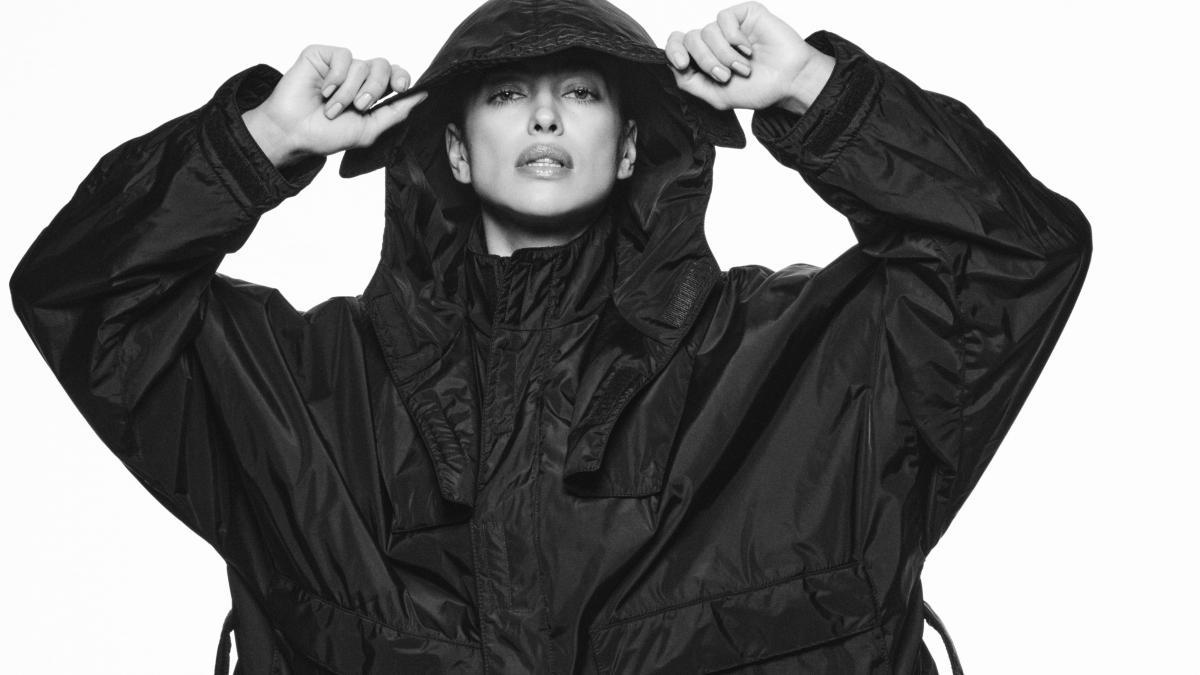
On a challenging path to convincing big brands of their environmental responsibilities, textile giant Inditex and chemistry Basf announced on Tuesday the successful development new textile material aims to support this fight for the sustainability of a sector criticized for its large environmental impact. The new fabric was named Lupamide, and this is the first nylon which comes entirely from textile waste, according to both firms. Technology used Allows the recycling of polyamide 6 (or nylon 6) textiles. and transform them into new fibers and materials of the same quality as virgin raw materials. For neophytes, the appearance of the fabric is very similar to raincoat. Polyamide 6 production plants are located in Europe, Asia and North America.
Banner Inditex Zara On Tuesday, the company released a jacket made entirely from Loopamid fabric. This is the first circular solution for nylon clothing made entirely from textile waste and promises to be beneficial for manufacturers looking to combine business profitability and a clean image with sustainability goals. All parts of this Zara jacket, including the fabric, buttons, padding, Velcro and zippers, are made from Loopamid.
bet on roundness This is a far-reaching economic strategy that is fundamental to the future viability of companies. Basf plans to double its sales related to circular economy solutions to 17 billion euros in 2030. Circulating raw materials, new generation materials and new business models are the three fundamental axes of development for Basf in this area.
Inditex aims to ensure that by 2030, 100% of its textile products are made exclusively from materials with a lower environmental impact. As part of this commitment, the Galician group expects that 25% of textile fibers will be produced from novel materials that do not exist today on an industrial scale, 40% from recycled materials and 25% from fibers from organic agriculture and regenerative materials. .
With the help of Loopamid, Basf has developed innovative solution to improve cycleability in the fashion industry and recycle polyamide 6 textile waste. With the ability to accept all fabric blends such as PA6 and elastane, the technology behind Loopamid allows post-industrial and post-consumer waste to be recycled from textile to textile. The fibers and materials can be recycled over and over again. In this case, the characteristics of the resulting material are identical to the characteristics of the primary polyamide.
Processes
The use and implementation of Loopamid is not an exclusive feature of Inditex. ModaRe, a clothing collection program run by Caritas, separates and sorts discarded textiles into new raw materials. The Italian company RadiciGroup has been working on a process for turning Loopamid polymer into different types of threads with different characteristics. Japanese multinational YKK fastener companies and multinational Velcro companies also played a critical role in using Loopamid to create plastic components for zippers, buttons and Velcro fasteners. The Spanish companies Uniter, Tessitura Vignetta (from Italy) and Freudenberg and Gütermann (from Germany) also took part in this project, developing other clothing components such as internal labels, fillers and sewing threads using Loopamid.
Javier Lozada, director of sustainability at Inditex, believes that the development of Loopamid “is the first step towards a circular solution; however, the industry needs to promote new collection and recycling capacity to close the loop and scale up post-consumer waste recycling.” Ramkumar Dhruva, president of Basf’s Monomers division, says the jacket produced by Inditex “is proof that circularity is possible and we are committed to further driving the sustainable transformation of the textile industry.”